Lawn care is a tough job. Not only is it physically challenging but technicians are mentally tested everyday in the field – from having to know mix rates to identifying plant and weed species.
Preparing technicians for the daily grind can be even more difficult. For weeks or even months, lawn care operators (LCOs) must review with trainees basic mathematics that many haven’t seen since grade school, teach proper safety procedures and educate their new employees on regional and federal environmental laws.
This translates into a lot of time and money for LCOs, so having a comprehensive training program to get the best return out of their investment is essential. Otherwise, companies become strapped with employees who are unprepared for the daily hurdles.
BACK TO SCHOOL. Imagine being away from school for more than 10 years and having to relive those dreaded story problems that caused cold sweats before a test. Technicians in training must know similar calculations before taking a related exam, which can sometimes be a challenge.
"The area they have the biggest problem with is math – doing the calculations to determine application rates, determining the amount of active ingredient per 1,000 square feet or per maximum labeled rates," says Dan Warehime, vice president of Senske Lawn & Tree Care, Kennewick, Wash. "The small amount of math associated with those things can be confusing to someone without a lot of background in those areas."
Some companies provide a refresher course on applicable math problems before state-required testing. Prior to the test, Senske Lawn & Tree Care trainees receive state-issued handbooks to review possible test material. The classroom and field training are conducted by a salaried supervisor, and the trainees are paid $9 to $10 per hour for the two-week training period. They review the handbook for two to three hours during the first three or four days of training, Warehime says.
Supervisors then administer a practice test at the end of each chapter. At Senske Lawn & Tree Care, an employee might see the following problem on a test: "The label reads, ‘Apply 1.5 ounces of this product in 1 to 10 gallons of water per 1,000 square feet. How much of this material will you put in a 100-gallon tank if you are going to apply the product at 4 gallons per 1,000 square feet?’"
Then, for regulations, employees may be asked questions like, "Which department enforces pesticide regulations while they are being transported on the road?" Warehime says.
Senske Lawn & Tree Care trainees take three tests with 100 multiple-choice questions, which are administered by the state where they’re located. The company has locations in four states, which include Washington, Oregon, Idaho and Utah, and tests range in cost from $60 to $120. The first test covers laws and safety, the second is ornamental and weed control and the third is ornamental insect and disease control.
Senske Lawn & Tree Care covers test fees and study manuals and any travel costs incurred on the first two tries. The company allows technicians three chances to pass the test, Warehime says. Employees cover all costs on the third test and are terminated if they still cannot pass. "That either tells me they don’t care to study or they can’t mentally comprehend the materials to pass it," Warehime says.
Senske’s annual training costs total $5,000, which includes staff fees, some airline expenses, lodging, food and facilities. Trainees receive 20 hours of classroom instruction and 60 hours in the field before taking the test.
Technicians at Denver, Colo.-based Swingle Tree & Lawn Care spend one week in the classroom where they’ll learn weed and turf identification, proper pesticide use, pesticide safety and pesticide formulations before supervisors administer a state-mandated test, and technicians with passing grades are allowed in the field, says Swingle Director of Operations John Gibson. Classroom size is usually 10 students to one instructor, who is a staff supervisor, according to Gibson. The first round of classroom training prepares Swingle technicians to become verifiably trained technicians (VTT). In Colorado, technicians must receive at least 24 hours of classroom instruction and 40 hours in the field before they can conduct applications with a supervisor present.
STAYING SAFE |
There’s potential danger at every corner for lawn care applicators if they companies make issues such as driver safety, proper mixing procedures and spill response a major part of their training programs. Massey Services, Maitland, Fla., provides a defensive driving course as part of the company’s basic training, which is a three-day course taught at the corporate office, says Adam Jones, vice president and director of quality assurance. Massey Services technicians review basic safety fundamentals with a service manager or experienced technician. Some topics include the importance of wearing a seat belt, how to check the vehicle before moving it and the proper speed limit to abide by in subdivisions. Also, the company tells drivers to make sure they have at least three seconds of reaction time between other drivers. This can be accomplished by driving slightly slower than the posted speed limit in residential communities, Jones says. "Even though the speed limit may be 25 or 30 mph, that speed seems like 100 mph to somebody standing on the side of a road with a child next to them, so we try to focus on driving no faster than 20 mph in a neighborhood," he shares. "That gives you plenty of reaction time in case somebody should dart out in front of you." Stopping distance can become an issue for employees who have never driven a truck, particularly one carrying 600 gallons of water, says Dan Warehime, vice president of Senske Lawn & Tree Care, Kennewick, Wash. In addition to reviewing stopping distances, Senske Lawn & Tree Care technicians are trained to make sure their truckload is properly secured and that their signals and breaks are working, Warehime explains. They also must report any mechanical problems. "It is amazing how some technicians will continue to drive a vehicle that has a mechanical failure of some kind without reporting it," he says. Another challenge new technicians face is driving without a rearview mirror. Senske Lawn & Tree Care supervisors encourage trainees to look out their side mirrors when backing up. "Most accidents occur when backing up, so we need to educate people on putting the vehicle in a position where you don’t have to back up," Warehime says. Pre-employment driving record checks can also help prevent accidents. Swingle Tree & Lawn Care, Denver, Colo., won’t accept anybody with more than two moving violations two years prior to employment or any major offenses in the last five years, such as drunken driving arrests, says the company’s Director of Operations John Gibson. During the first two days of training at Swingle Tree & Lawn Care, technicians take a driving test on standard and automatic transmission trucks, Gibson says. After the test, technicians take a two-hour defensive driving course and watch a video that discusses required stopping time for heavy loads, according to Gibson. When accidents do happen, employees need to know standard procedures, especially when there’s a spill. The company’s technicians are trained on spill response and have a page in their route books dedicated to spill procedures, Gibson says. Supervisors there teach technicians how to shut off valves in the truck, how to dam the fluid and to contact a supervisor once the situation is somewhat contained. Massey Services employees are instructed how to contain a spill, how to help any injured people and move them from the scene, how to report the incident and document it correctly, how to determine the amount of material lost, how to respond to media inquiries and what to do if emergency response teams arrive. As Jones explains, "The last thing we want is the fire department to show up and hose down a chemical spill and run it down a storm drain." |
Swingle Tree & Lawn Care pays employees their regular rate during training, which is $9 to $18 per hour and supervisors receive their regular salary, according to Gibson.
After VTT certification, technicians have opportunities to move up in rank by obtaining either a certified operator’s license or a qualified supervisor’s license – the highest-ranking certification. The company usually won’t offer the certified operator’s test or qualified supervisor’s test until an employee has six to eight month’s experience, Gibson says. Without the certified operator’s license or qualified supervisor’s license, technicians cannot make applications without supervision.
Qualified supervisors can evaluate pest problems, recommend control products, sell application services, operate pest-control devices or supervise others in any of these functions, according to the Colorado Department of Agriculture. Certified operators can only apply restricted-use pesticides without the presence of a qualified supervisor.
The tests for the qualified supervisor’s license and the certified operator’s license cost $100 each and are administered by the Colorado Department of Agriculture, Gibson says. Swingle Tree & Lawn Care technicians purchase their own $40-training manuals and are reimbursed for test fees if they pass, Gibson says. They pay for their own licenses, which also cost $100, because they’re considered the technicians’ property. Technicians receive 50-cent-per-hour raises for certified operator’s licenses and $1-per-hour advances for qualified super-visor’s licenses, Gibson says.
At Massey Services, Maitland, Fla., technicians are first assigned 45 minutes to an hour of reading material each night during their two-week training period, says Adam Jones, vice president of quality assurance. In the classroom, new hires learn how to identify different grass plants, 15 to 20 most common ornamental plants, soil pH and structure, equipment maintenance and application procedures.
In Florida, lawn care companies must document that technicians have received at least 40 hours of classroom training before they can obtain an identification card, according to Jones. Florida does not require that technicians take a state-administered test. The training is documented when supervisors sign off on the identification card application.
The entire training process costs Massey Services at least $1,200 per day in lost revenue to have supervisors teach the courses and to outfit trainees in uniforms and safety equipment, according to Jones. Trainees are typically paid about $65 per day during training, and class sizes are usually 25 to 30 people, Jones says. Instructors are typically staff managers who receive their regular salary or university professors. Massey Services pays a $200- to $400-donation to the professors’ universities for their services, according to Jones. "Everyday that the service person is not out being fully productive that costs us in terms of lost revenue," Jones explains. "We make it up with other people. Other technicians have to carry the load or management has to help carry the load."
Jones says there’s no way to offset training costs and that they’re just accepted as a business expense. He estimates that 99 percent of technicians make it through the two-week process and that the highest turnover rate usually occurs after three to six months, adding that the physical and technical demands can contribute to employee losses during this time.
IN THE FIELD. Seasoned lawn care operators know technicians learn best through experience. At Massey Services, trainees get hands-on practice after just three days. During the first three days of training, new hires watch a supervisor perform an entire service stop – from routing their calls and driving safety to actually performing the application, Jones says.
After the observation period, trainees practice applications on a 40-by-25-foot-company driveway with a supervisor at their side. The driveway is diagramed with starting and end points and strategically placed dots that represent patches, which the employees cannot miss, Jones explains.
Field training teaches applicators proper arm movement, walking pace and how to turn and overlap properly, Jones says. On liquid applications, for instance, trainees are timed on spraying pace. The company applies 3 gallons of product per 1,000 square feet, and calibrates its trucks to pump 3 gallons of liquid per minute, meaning trainees must treat that area in one minute, Jones explains.
"They keep doing it until their pace is proper, until their overlap is accurate and until their arm movement is accurate, and they’re supervised through the whole process," Jones says. "They’ll probably make 20 to 30 trips through that area before they do it properly. Some people do it in five, but they’ll probably practice for a good hour and a half or two hours until they feel comfortable and understand the dynamics of it."
For arm movement, trainees learn how to hold the spray gun at a certain angle and move at the right pace for optimal particle distribution. "The most common mistakes are in the proper arm movement and making turns," Jones says. "We usually get them dialed in on walking pace pretty quickly, but getting them to turn the right distance can take longer."
When turning, technicians learn how far to overlap, Jones explains. Technicians learn this by walking in a straight line and turning in a square pattern. They must also pick a distant target and walk directly to it without wandering and are instructed to keep their head up instead of looking at their feet.
Senske Lawn & Tree Care technicians go through a similar field training procedure. Supervisors first train technicians on turf and asphalt surfaces at the company’s facilities, Warehime says. At the facility, supervisors demonstrate the correct technique to the trainees. For instance, they’ll tell the technicians there must be equal amounts of material delivered to both sides as they walk because right-handed people tend to be heavy on the left, Warehime says. "Your right wrist bends easily to the left but not well to the right," he explains. "Too much material to one side as you walk is the major cause of striped lawns."
After observing, trainees take a dry run with an empty tank and gun to master the footwork and wrist movement. They then spray water on the asphalt so they can see their pattern before moving onto the lawn where they get a feel for the edges and undulations in the yard, Warehime says.
Trainees then go to a customer’s property where they observe for several yards before they begin spraying actual material on a portion of a lawn. Once a supervisor is comfortable with their spraying competency, trainees will spray an entire lawn and be checked for application rate.
When spraying, new technicians work from a truck and spray gun that are set to disburse 4 gallons per minute, which should cover 4,000 square feet, according to Warehime. Before the application, trainees will test their guns to make sure they’re delivering the proper amount. When a lawn is completed, they will check the meter to see how many gallons they applied to the pre-measured turf. An instructor will then provide the trainee with a feedback form, pointing out the light and heavy application areas.
Swingle provides trainees with field experience before any classroom training to "weed out" candidates having second thoughts, according to Gibson. Swingle Tree & Lawn Care supervisors take new technicians through a route, teach them how to set up their trucks and have them perform applications during the first two days of training. The company conducts field training on a customer’s lawn where a supervisor stays by the technician’s side for every step, Gibson says.
New Swingle Tree & Lawn Care technicians first observe a supervisor who gives them a recommended pace based on their height, which impacts the length of their stride. Trainees are then taught how to calibrate their spreaders to match their pace. The company’s employees must know some basic math to calculate their pace. For instance, technicians are supposed to use 4 pounds of fertilizer per 1,000 square feet, Gibson explains. So if a technician applied fertilizer to 110,000 square feet that day, that technician should have used 440 pounds of fertilizer.
"If they find out they used 390 pounds of product that day, then we take the difference, which is 50 pounds, divide that by 440, and find out they’re roughly 12 percent light in their product usage for the day," Gibson says. "Then we tell them they have to be within 10 percent. We’d actually like them to be within 5 percent of their usage, but we know that our lawn measurements aren’t 100 percent accurate, so we give them that fudge factor."
Employees at Baltimore, Md.-based Pro-Lawn-Plus typically go through a 30-day field apprenticeship before taking over their own routes, says President Mark Schlossberg. Trainees there also learn how to calibrate spreaders, keep a constant walking speed and mix products through observation and experience. One of the more critical training segments occurs when technicians learn how rate ranges vary depending on weather conditions. "With some of the broadleaf herbicides, rates can be lower or higher with weather changes, so we have to adjust to that quickly to avoid burning shallow-rooted grasses," Schlossberg says.
CUSTOMER RELATIONS. The old saying that "the customer is always right" may not always be true, but technicians need to follow it anyway if they want to maintain business, Schlossberg says. Pro-Lawn-Plus instructs technicians on how to properly deal with neighborhood and customer complaints.
Pro-Lawn-Plus supervisors tell new hires that they can’t take complaints personally and to empathize with customers instead of getting defensive. The company also encourages positive neighborhood relations by telling technicians to be sensitive to property mangers’ and tenants’ concerns when spraying nearby. Technicians learn they should try to accommodate sensitive neighbors by notifying them prior to applications.
Knowledge is sometimes the best way to prevent such customer-service problems, adds Tim Doppel, owner of Atwood LawnCare, Sterling Heights, Mich. "A new trainee will typically be amazed at just how passionate the customers are about their lawns, and they have to respect that passion and respond to it," Doppel says. "Once they understand how important people’s lawns are to them, they usually respond well."
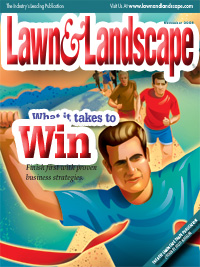
Explore the November 2004 Issue
Check out more from this issue and find you next story to read.
Latest from Lawn & Landscape
- Perfecting the spring kickoff
- Sell 24/7 with Online Chatbot
- Volvo Construction Equipment updates L30, L35 models
- PERC hires director of autogas business development
- Student Spotlight: Emily Braithwaite
- Sunseeker sets sights on Orion X7
- Fight the bite
- Attentive.ai’s next webinar to touch on revenue recognition methods