
![]() Images courtesy of Banks Group |
In the windswept North of England, a naked lady draws a crowd. People from far and wide come to caress her curves, touch her hands, gaze upon her face. Even a princess has made the trip to witness her bare wonder.
The Lady of the North is the world’s largest human landform. Her reclined body is a quarter mile long. Her voluptuous contours arch 100-feet high. It takes roughly 20 minutes to walk the three-quarter mile-long outer path around the landform, with more than another three miles of walking paths winding through the sculpted body.
The sculpture is the centerpiece of a 47-acre park called Northumberlandia, located just west of Cramlington in the county of Northumberland, not far from the ruins of ancient Roman forts and Hadrian’s Wall.
The site borders a surface coal mine operated by the Banks Group. Rather than just building a berm as a noise and visual buffer for the mine, the landowner decided to create a public park. The project took more than two years to build and cost £3m (three million British pounds).
“The Estate has always tried to play a proactive role in enhancing the local community in a wide range of ways, and the opportunities that this scheme will create will bring many benefits to the local people in terms of leisure, nature conservation, tourism and public health,” says Bob Downer, chief executive of Blagdon Estate, the landowner.
The scheme worked. Not only has the Lady become an international tourist attraction, but Princess Anne, a member of the British Royal Family, personally dedicated the site in a ceremony in September.
The Lady of the North was designed by Charles Jenks, the famed landscape architect responsible for high-profile projects such as Olympic Forest Park in Beijing. Jenks’ original plan called for The Lady’s features to be carved from the coal mine’s waste material, but the material alone proved unstable. The team had to find a way to create cohesion and structural integrity in order to form the head, hands, feet and breasts of the sculpture.
The Banks Group brought in Geosynthetics Ltd., a British manufacturer of geotextiles and geogrids, structurally reinforcing meshes and fabrics that stabilize soils. Geosynthetics contacted Phil McGoldrick, managing director of InterGEO Services Europe, a specialized geotechnical contracting company based in Ireland. (InterGEO Services was founded in the United States by Archie Filshill, Ph.D., in Trevose, Pa.).
Together, InterGEO Services Europe and Geosynthetics Ltd., came up with a plan to build up, reinforce and stabilize the soils. Strategically placed geogrids were used to add strength to the structure. Geotextiles held the loose soil in place to prevent erosion.
![]() Images courtesy of Banks Group |
Working from Jenks’ 3-D model, and using a design software program called ReSlope, for about eight months McGoldrick worked on the geometry to create a design plan. During construction, batter rails with digital readouts staked out the curves of the body. Highly experienced bulldozer drivers, all of them employees of the mine with 30 years or longer on the job, shaped the contours. “They have the invisible touch,” McGoldrick says. “They know how to read the batter rails. They’re phenomenal guys. You could not have done a project like this without them.”
Flat areas of the structure, about 70 percent of the grassed landform, were hydroseeded with red fescue turf seed. Other areas, such as the head and hands, were built and then immediately sodded with red fescue grown on erosion mats for instant soil stabilization. On the flatter areas, McGoldrick says the sharpest slope is approximately 22 degrees and can be mowed normally. The steeper slopes of the head approach 70 degree angles.
“The chin, the nose, the sides of the temples will never be mowed. The first growth will only grow to a certain length. It’s the first growth so if you don’t touch it, you’re fine. Like when you start shaving as a kid, once you shave, the more it grows,” McGoldrick says.
Even though construction went well, McGoldrick says the team did encounter one unexpected issue.
“The main challenge was when you’re using a pure quality material, this waste material, they tend to be quite soft and they tend to absorb a lot of water. In North England, we have a lot of rainfall. So when you have a lot of rainfall and you’re trying to build a structure in soil, you have a lot of mud. There was a lot of settlement of the structure because when you add water to soil, the soil reduces in strength. Once the project was started, we had a bit of a problem with the water and a lot of seepage of water. So, halfway through the project they had to develop a new internal drainage system within the structure,” McGoldrick says.
Perforated plastic pipes, wrapped in geotextile to keep the soil from clogging the holes, were buried in the structure. The drainage pipes were tied into the lagoons on the property.
“The lagoons started off as ornamental, but in the end they actually became functional. The lagoons were increased in size by about 25 percent to take away the water and to become drainage lagoons. When it rains on the structure now, you get a lot of runoff into the lagoons,” McGoldrick says. “The combined design and construction experience of InterGeO & Geosynthetics Ltd. provided the client with an excellent final finished sculpture to the contract specification,” says Maria Patricia Guerra Escobar, senior engineer at Geosynthetics Ltd.
And meet the tolerances they did. “I think, on the nose, on the highest tip of the head, we were two-inches too high. That was it. We built that whole outline of that face. Everything was perfect, everything was exactly to zero tolerance, except the tip of the nose was two-inches out,” McGoldrick says. “For me, that was the most uplifting aspect, that we could actually build it to such a detailed tolerance with pure quality.”
The author is a freelancer based in Mount Vernon, Wash.
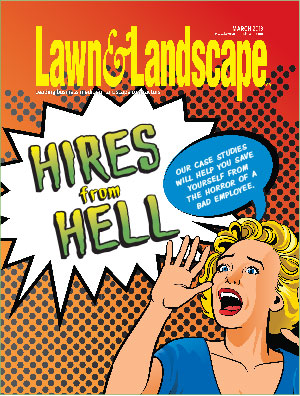
Explore the March 2013 Issue
Check out more from this issue and find your next story to read.